The first wave of the COVID19 pandemic asked a lot of all hospital staff. From doctors and nurses to porters and housekeepers, life on the frontline of hospital care took a rapid and unexpected twist in just a matter of days, but what of the other teams working behind the scenes?
Today is Clinical Engineering Day, so it seems only right to highlight how the work of this small but perfectly formed team supported frontline staff, enabling the carers to continue caring for critically ill patients while the techie bits were taken care of.
Professor Andy Beavis, head of medical physics for the trust, takes up the story:
“Every one of us working for the trust was impacted in some way by COVID19 back in the Spring, and many people stepped forward to contribute their skills in different ways.
“One of the great positives that came out of the situation was the spirit of how staff pulled together and worked to deliver services in the middle of the biggest challenge we have ever faced. For me, nowhere was this more evident than within our own clinical engineering team.”
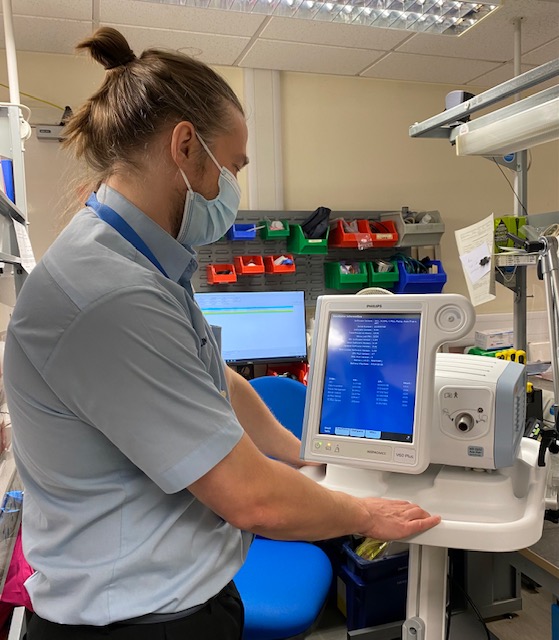
Clinical engineer Dean Young tests a ventilator
At any given time, this team of 36 engineers has an enormous inventory of medical equipment to service and maintain, from equipment used in the care of premature babies right through to the care of older people. Among the items on their lists are heart rate monitors, thermometers, pressure relieving mattresses and ventilators, anaesthetic machines and ultrasound scanners, and the list is always increasing. Last year there were 22,000 pieces of equipment in the inventory, but with the arrival of COVID-19 came a growth in the amount of equipment being used, and that figure is now closer to 30,000. The team must also ensure items don’t get stuck in the service cycle, and that equipment is freely available to wards and teams whenever and wherever it’s needed.
Towards the start of 2020, as the scale of the COVID19 challenge was becoming more apparent and as ventilators became the most sought after item of the year to date, the team soon realised that demand for their knowledge and skills within the trust would skyrocket.
“From the outset, the team was worried about the availability of equipment for frontline clinical teams such as ventilators and infusion pumps, and the associated implications for patient care; such items were considered essential in the initial management of the effects caused by the virus,” Andy continues.
“A significant part of the engineers’ work in the early weeks, therefore, was helping to source, locate, collect and transfer equipment from wards and theatres to those parts of the hospital which were most in need. The engineers made sure those staff on the receiving end were briefed on how to use the items and manage any risks, but it soon became apparent that there was still an unfamiliarity for some staff around using equipment in ways they may never have done before.
“At this point, this small team of engineers put their own convenience to one side and decided to establish 24/7 technical cover in order to support and reassure those staff working on the frontline of the coronavirus effort. This was not without its challenges as the team is ordinarily designed to work a ‘standard’ five day working week, but support for our patients and intensive care staff was central to all our discussions, and the engineers were really keen to step up and play their part.”
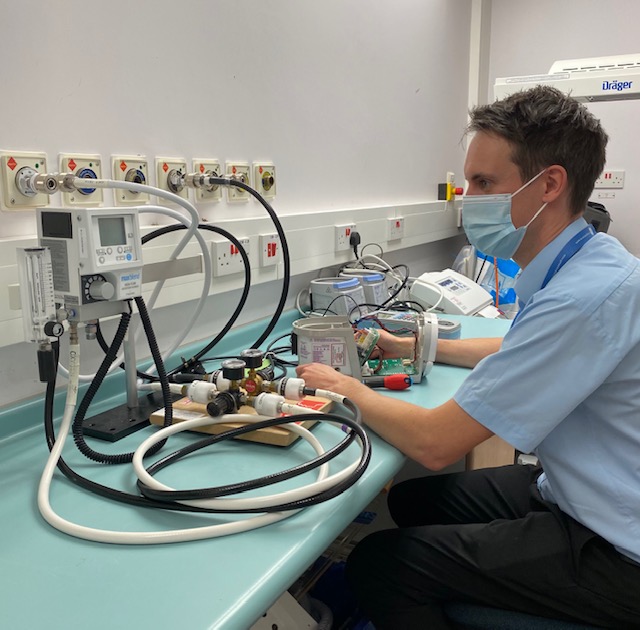
Andrew Mills sets about fault-finding on a humidifier
Almost immediately, the team agreed and put in place a split shift system, providing on-call cover throughout the night for more than 16 weeks.
“One of the other issues we had to overcome was that the team members each had different specialisms and areas of expertise, meaning not all of the team were familiar with troubleshooting or maintaining all types of systems. Before the on-call system was started, the team overcame this by developing service packs of information and cross-training each other to ensure they, and the staff they were supporting, could be confident that any given problem could be dealt with.
“While delivering this high level of support, the team also ensured that extra new equipment being supplied to the trust to support the COVID effort was brought into use as soon as possible, and kept more routine non-COVID equipment maintenance going.
“The team would say they simply provided what was expected of them at such a time, but what I saw was a genuine willingness to help and a real commitment to supporting others.
“Just like many other frontline workers, they too sacrificed their own personal or family time to support the COVID19 effort. The team underwent appropriate Fit testing and PPE training to be able to work in the most high-risk areas around our hospitals and ensure patients could receive the high quality care they needed. I’m incredibly proud of our clinical engineers.”